When you're searching for or designing the perfect seal for hydraulics, understanding the theory behind hydraulic seals is critical. From static and dynamic sealing to system motion, a lot goes into the creation and maintenance of hydraulic cylinders.
At PSP Seals, we not only source and distribute the highest quality seals, we also custom machine and create the right fit for all your sealing needs. Let's learn some more about hydraulic seal theory and don't forget to visit our store for all of your sealing needs.
What are the principles of hydraulic sealing?
For typical hydraulic cylinders, the basic hardware components that seals are installed into are pistons and rod glands. Seals will perform a wide range of function within these pistons and rod glands, and the measurements of the hardware determine the type and size of seal that can be used. Measurements used to define hardware include piston, bore, throat, rod, and groove diameters, as well as groove width.
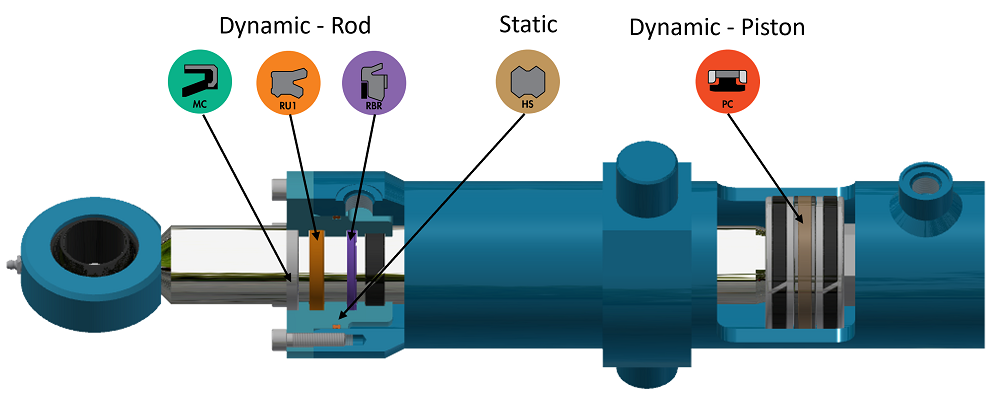
The motion of the equipment will also determine what kind of seal is needed. There are three types of system motion: reciprocating (back and forth linearly), rotary (rotating in one direction), and oscillatory (rotation back and forth). All types of system motion typically utilize both static and dynamic seals in different locations.
In a static sealing application, the relative seal-to-hardware contact remains stationary. Compressive forces generated when the seal is installed into the gland will create squeeze, which is critical to the performance of that seal. The better the seal conforms to the hardware, the less leakage or failure arises.
In a dynamic sealing application, the seal exhibits dynamic motion relative to the hardware. As this adds additional forces on the seal, dynamic sealing requires consideration of other factors such as friction, lubrication, and proper surface finishes; all critical for long-lasting and effective sealing.
WHAT FACTORS AFFECT SEAL PERFORMANCE?
The most common factors and issues that arise with sealing are pressure, extrusion, temperature, friction, wear, stability, and compression set.
PRESSURE
With both static and dynamic sealing, system pressure applied during operation is an additional source of force on the seal, making seal profile, fit, and material selection critical to success.
Pressure in sealing is generated from two sources, mechanical squeeze and system pressure. Low pressure systems rely more on the shape of the seal, while high pressure systems rely more on the forces applied by seal squeeze and system pressure. A seal must be appropriately designed to suit the operating pressure of the system, with considerations on material type and profile.
EXTRUSION
Extrusion is the seal deformation that occurs when pressure forces the seal into the hardware extrusion gap. This can be exacerbated by having a larger e-gap than is recommended, dynamic motion pulling the seal into the gap, excess temperature acting on the seal, and operation at system pressures above recommended limits.
FRICTION
Friction is generated from multiple sources in a sealing system: The radial force exerted by the seal from squeeze, as well as operating fluid pressure. Some factors that influence friction include seal material, hardware surface roughness, temperature, and lubrication. Friction may be reduced by reducing the seal’s cross section, decreasing lip squeeze, changing the seal material, reducing system pressure, or improving lubrication.
COMPRESSION SET
Compression set occurs when a seal fails to return to its original size after release from a constant compressive load. Over time, this can reduce a seal’s ability to function properly and cause leakage or failure. Compression set typically occurs due to temperature or pressure exposure above recommended limits, or for extended periods of time. Selecting the correct seal material and profile for the application is key to lasting seal life.
WHAT IS THE BEST SEAL DESIGN FOR PERFORMANCE?
When considering the design of the seal, there are three main focus areas for optimal performance: seal profile, sizing, and material selection. Seal profile addresses the shape and type of seal used, to properly choose the best style of seal for the intended purpose. Correct sizing to the hardware ensures the seal has appropriate squeeze, gland fill, and interference for functionality. Material selection will ensure the seal is properly suited for the temperature, pressure, and fluid compatibility in the application. All factors are critical to design for performance and must be considered for sealing success.
Let Psp seals help you find your perfect Seal
PSP Seals, LLC is your connection to the best-in-class sealing products. Our online purchasing makes it easy to find the seal you're looking for in the right style, material, and shape plus you can rest assured you're getting the best service from the experts on sealing.
Don't see what you're looking for right away? With several decades of combined experience, our engineering team is ready to assist you in selecting or designing the right seal for any need that arises. Contact our engineering team at engineering@pspseals.com.